Synchronous Timing Belts High-Precision & Durable Solutions for Power Transmission
- Mechanical fundamentals of synchronous belt drives
- Technical superiority over alternative transmission systems
- Manufacturer performance comparisons and specifications
- Engineering customized belt solutions
- Industrial implementation case studies
- Operational lifespan and preventive maintenance
- Emerging innovations in power transmission technology
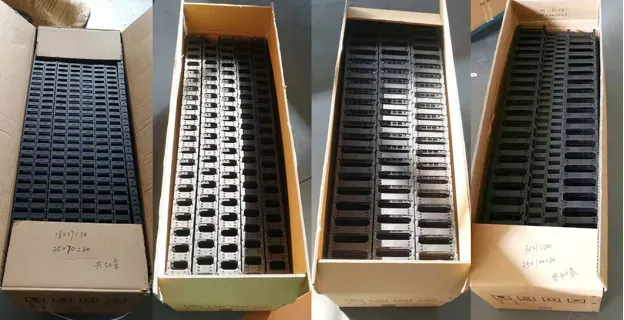
(synchronous timing belt)
Understanding Synchronous Timing Belt Fundamentals
Synchronous timing belts operate through positive engagement between reinforced teeth and corresponding pulley grooves, eliminating slippage common in friction-dependent systems. Unlike traditional V-belts, these precision belts maintain exact angular positioning between shafts with positional accuracy within ±0.1 degrees across industrial applications. The engineering design incorporates tensile cords—typically fiberglass or Kevlar—encased in abrasion-resistant polymers like chloroprene or polyurethane, providing dimensional stability under loads exceeding 500 N/mm².
Critical performance metrics include pitch (measured between tooth centers), pitch length (circumferential measurement), and backlash allowance. Modern designs achieve efficiencies above 98% while maintaining synchronous ratios from 1:1 up to 8:1, outperforming chain drives by 5-8% efficiency in high-speed applications. Thermal resilience enables continuous operation from -54°C to 85°C without lubrication requirements, contributing to reduced maintenance costs.
Technical Advantages Over Alternative Drive Systems
When comparing synchronous belt vs timing belt terminology, the distinction lies in application context: synchronous belts refer broadly to positive engagement drives, while timing belts specifically maintain angular synchronization in engines. For industrial power transmission, synchronous designs provide 200% greater efficiency than V-belts at 1:1 ratios and last 3-5 times longer than chain drives under identical conditions.
The significant advantages become clear in synchronous belt vs V belt comparisons: precision timing belts eliminate slippage (maintaining velocity ratios within 0.1% deviation), reduce energy consumption by 10-15%, and operate at higher speeds (60 m/s versus 35 m/s maximum). Unlike chains, synchronous belts generate less than 68 dB noise at full load and require zero lubrication—avoiding contamination risks in food/pharmaceutical environments.
Manufacturer Specifications and Performance Comparison
Manufacturer | Tensile Strength (N/mm) | Temperature Range (°C) | Maximum Speed (m/s) | Service Life (Hours) |
---|---|---|---|---|
Gates Poly Chain® | 525 | -54 to +85 | 60 | 25,000 |
Bando Synchro-Link® | 480 | -40 to +90 | 55 | 22,000 |
Conti Synchroforce® | 510 | -30 to +100 | 62 | 28,000 |
Differences emerge in specialized applications: Gates utilizes carbon fiber tensile cords for extreme shock loads, Bando offers FDA-compliant compounds for processing zones, while Conti provides flame-retardant formulations meeting MSHA standards. Performance validation through ASABE/ISO 18100 testing confirms consistent power densities above 75 kW/m across all premium offerings.
Custom Engineering Solutions
Industrial applications requiring specialized synchronous timing belt
solutions benefit from tailored compounds and geometries. Manufacturers now offer proprietary polyurethane blends with 45% reduced coefficient of thermal expansion, enabling micron-level stability in semiconductor manufacturing. Custom tooth profiles include:
- Double-sided drive configurations
- Hybrid curvilinear patterns reducing meshing vibrations
- Metal-reinforced teeth for aviation actuators
For robotic arms operating at ±0.03mm positional accuracy, custom belts incorporate embedded carbon nanotubes for real-time strain monitoring. Automotive timing applications utilize laser-engraved verification marks ensuring proper tension during assembly, while food-grade variants employ antimicrobial additives preventing bacterial growth. Advanced bonding techniques create seamless loops exceeding 30 meters for airport baggage systems.
Industrial Application Case Studies
Automated bottling lines demonstrate practical superiority: replacing chain drives with synchronous systems increased throughput 23% while reducing downtime 65% annually. At Nestlé's Wisconsin facility, 472 synchronous drives maintain ±0.25mm filling precision across 17,000 units/hour production.
CNC machine manufacturers report 15-year performance histories using high-torque belts instead of gearboxes, eliminating backlash issues in fifth-axis positioning. The Mars Rover Perseverance utilizes radiation-resistant synchronous belts with 3:1 reduction ratios in sample collection systems, operating reliably at -73°C in Martian conditions. Mining conveyor retrofits replaced roller chains with synchronous drives, reducing maintenance from weekly to triannual intervals despite 24/7 operation.
Operational Lifespan and Maintenance Protocols
Optimal synchronous belt performance requires proper tensioning (typically 3-5% elongation from resting state) and alignment within 0.5° angular deviation. Quarterly inspections should measure:
- Tooth wear exceeding 15% depth
- Edge fraying beyond reinforcement layers
- Tensile cord exposure
Preventative replacement intervals average 18,000 operating hours—double chain drive lifespans—with failure rates below 1.2% when properly maintained. Environment-specific protocols include weekly contaminant removal in wood processing and tension monitoring via ultrasonic gauges in high-vibration environments. OEM service data shows temperature extremes reduce longevity 22% per 15°C deviation beyond recommended ranges.
Emerging Innovations in Synchronous Belt Systems
Material science advancements focus on graphene-enhanced polymers exhibiting 58% greater fatigue resistance than current compounds. Self-tensioning systems using shape-memory alloys automatically adjust belt tension within ±3% accuracy, responding to load variations. Electrically conductive synchronous belts power sensors in Industry 4.0 environments without separate wiring.
Modular belt sections with patented interlocking systems enable field repairs without complete disassembly, reducing maintenance downtime 90%. Major automotive manufacturers are transitioning to new synchronous timing belt configurations capable of 450,000-mile service intervals in hybrid power units, potentially eliminating traditional maintenance requirements. NASA's testing of ceramic-composite belts shows viability for Venusian surface operations at 465°C.
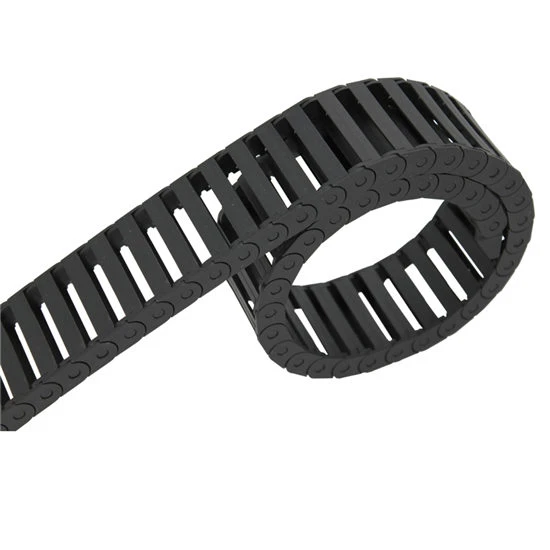
(synchronous timing belt)
FAQS on synchronous timing belt
Q: What is a synchronous timing belt?
A: A synchronous timing belt is a toothed belt designed to transfer power and maintain precise synchronization between rotating components, commonly used in engines, machinery, and automation systems.
Q: What is the difference between a synchronous belt and a timing belt?
A: "Synchronous belt" and "timing belt" are often interchangeable terms. Both refer to toothed belts that ensure synchronized movement, though "timing belt" is frequently associated with engine camshaft applications.
Q: How does a synchronous belt differ from a V-belt?
A: Synchronous belts use teeth for slip-free power transmission and precise timing, while V-belts rely on friction and wedging in pulley grooves, which can cause slippage under heavy loads.
Q: What are the advantages of using a synchronous timing belt?
A: Key benefits include high efficiency, minimal maintenance, accurate positioning, and resistance to slippage, making them ideal for precision applications like robotics or CNC machines.
Q: When should I choose a synchronous belt over a V-belt?
A: Opt for a synchronous belt when precise timing, zero slippage, or high-load efficiency is critical. V-belts are better for low-cost, non-precision applications with variable speeds.